一、当工业之眼进化:从CCD到3D视觉的代际跨越
能力维度 |
传统CCD工业相机 |
迁移科技3D视觉系统 |
信息维度 |
二维平面像素 |
三维点云坐标+纹理信息 |
检测精度 |
±0.1mm(平面方向) |
±0.02mm(空间全向) |
数据丰富度 |
单帧200万像素 |
每秒800万点云+RGBD融合 |
环境适应性 |
需专用背光系统 |
支持自然光动态补偿 |
在某手机中板检测车间,我们见证了这样的技术迭代:传统CCD方案需要6台相机多角度配合才能完成的平面度检测,迁移科技EC-V500视觉系统仅需单相机即可完成三维形貌重建。检测时间从3.8秒缩短至0.9秒,缺陷检出率从92%提升至99.97%——这正是三维视觉对二维成像的维度碾压。
二、二维视觉的四大能力边界与破局路径
- 深度缺失之痛:某汽车零部件企业因平面检测盲区导致的批次性缺陷损失达1200万元/年
- 效率天花板:光伏行业CCD检测系统处理速度长期卡在1.2秒/片的物理极限
- 柔性不足之困:医疗器械企业每次换型需重新搭建光学系统,年均浪费368工时
- 数据孤岛难题:某半导体工厂200台CCD相机产生的数据利用率不足15%
三、三维视觉技术穿透:构建工业质检新范式
-
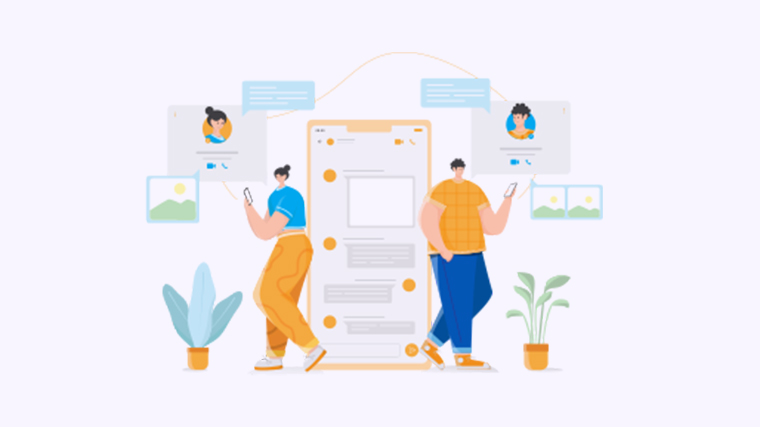
基础功能重构
- 0.6μm空间分辨率实现微观形变检测
- 多光谱融合技术攻克金属反光表面成像难题
- 智能曝光控制算法适应0.1-100,000Lux照度变化
-
场景方案升级
- 为某连接器厂商定制的三维检测系统,将平面度检测效率提升47%
- 在锂电池极片检测中,实现0.02mm级波浪边缺陷的实时捕捉
- 通过三维数据建模,使汽车发动机缸体检测项目减少3道冗余工序
-
产业价值跃迁
- 推动3C行业质量成本占比下降1.8个百分点
- 帮助光伏企业年减少返工损失超2500万元
- 使精密模具检测效率突破"单日20模"的行业瓶颈
核心技术指标 |
客户价值维度 |
实证案例数据 |
120fps扫描速率 |
匹配高速产线实时需求 |
某SMT产线设备稼动率提升29% |
0.05°角度解析度 |
实现装配间隙精密检测 |
年避免错装损失超800万元 |
5Gbps数据吞吐 |
支撑全流程质量追溯 |
产品溯源效率提升60倍 |
四、标杆案例:解码某新能源汽车电池盒检测革命
改造维度 |
传统CCD方案 |
3D视觉解决方案 |
价值增量 |
检测项覆盖率 |
72% |
98.5% |
年减少售后索赔1600万元 |
单件检测耗时 |
42秒 |
9秒 |
释放30%产能潜力 |
数据利用率 |
孤立存储 |
全流程MES对接 |
工艺优化周期缩短65% |
该项目创新性应用迁移科技的动态基准面技术,在2.5m×1.8m的大型电池盒检测中,将平面度、装配孔位、焊接质量等23项检测集成于单工位完成。系统运行首年即帮助客户减少质量成本1200万元,并成功通过IATF 16949认证审核。
五、下一代工业视觉的三大技术演进方向
- 正在研发的EC-V900系列将检测精度提升至亚微米级
- 基于深度学习的预测性质量控制系统进入实测阶段
- 跨设备视觉协同网络在某家电工厂实现98.7%的协同检测准确率