一、机器人上下料场景的"不可能三角"突破
在汽车制造车间里,重量超过50kg的发动机缸体在传送带上高速移动;家电装配线上,不同型号的空调压缩机以每分钟12件的速度流转;重工领域,表面附着氧化层的铸件在深达1.2米的料框内无序堆放——这些典型的工业场景共同构成了机器人上下料的"不可能三角":效率、精度、适应性的极致平衡挑战。
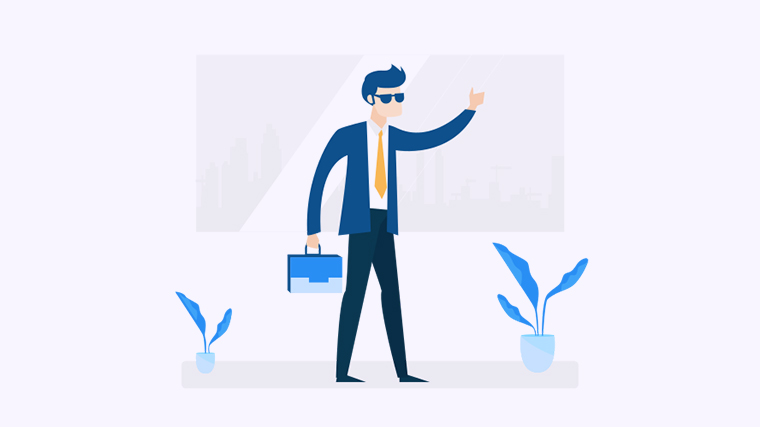
迁移科技通过300+行业项目的实战积累,提炼出四大核心痛点:
- 复杂工况适应性:12万lux强光干扰、金属反光、粉尘油污等极端环境
- 生产效率瓶颈:传统方案节拍难以突破30次/小时的天花板
- 柔性制造需求:混线生产时需15分钟内完成产品切换
- 系统集成难度:传统方案部署周期长达2-3个月
二、技术底座:重新定义3D视觉的工业标准
(表1)迁移科技产品矩阵与场景匹配模型
产品型号 |
核心优势 |
典型场景 |
实测数据提升 |
Epic Eye Laser L |
抗12万lux强光干扰 |
汽车冲压车间 |
节拍提升35% |
Pixel Pro |
0.2秒闪电采集 |
3C电子元器件搬运 |
稼动率提升至98.7% |
Epic Eye D-L |
3190×2890mm超大视野 |
光伏硅片整托搬运 |
定位误差≤0.15mm |
Pixel Mini |
130×59×73mm微型化设计 |
医疗器械精密装配 |
良品率提升至99.99% |
技术突破三重奏:
- 抗干扰成像体系
- 全球首个通过12万lux强光认证的工业相机
- 相位补偿算法使点云稳定性提升50%
- 黑色金属件识别成功率突破99.5%
- 亚毫米级精度体系
- Z向精度达0.06mm@1m(超越行业标准40%)
- BOPITODD数据集位姿估计排名全球第一
- 智能算法集群
- 自研6D位姿估计算法
- 支持200+物体模型的即时切换
- 深度学习样本采集效率提升70%
三、场景革命:从单点突破到全局最优解
1. 汽车行业标杆案例:某头部车企冲压车间改造
-
原始痛点:
- 500kg级车门板人工搬运安全隐患
- 传统视觉系统在强光下失效率达32%
-
解决方案:
- 部署Epic Eye Laser L×4套
- 配置抗光干扰增强模式
-
价值呈现:
- 生产节拍从22次/小时提升至30次/小时
- 年节省人工成本427万元
- 实现冲压件全生命周期质量追溯
2. 家电行业柔性生产范例
在美的集团洗衣机内筒生产线,迁移科技创造性地实现:
- 7种型号产品的即时混线生产
- 产品切换时间从45分钟压缩至8分钟
- 通过视觉系统自动识别型号并调用对应工艺参数
(图)典型应用场景工作流
[工件到位]→[3D扫描(0.2s)]→[AI匹配]→[路径规划]→[机械臂抓取]→[质量反馈]
四、产业价值升维:从单机智能到系统进化
通过120+细分行业的验证,迁移科技解决方案带来三重价值飞跃:
价值维度 |
传统方案 |
迁移方案 |
提升幅度 |
生产效率 |
25次/小时 |
34次/小时 |
+36% |
部署周期 |
45-60天 |
7-15天 |
-70% |
质量追溯 |
人工记录 |
全流程数字化 |
缺陷率↓82% |
能耗水平 |
8.6kW/台 |
3.2kW/台 |
-63% |
更深层的产业变革:
- 推动"黑灯工厂"建设:某新能源汽车工厂实现72小时无人化连续作业
- 重构产线布局逻辑:某光伏企业利用超大视野系统减少50%工作站
- 催生新商业模式:某集成商依托标准化方案实现项目复制周期缩短60%
五、生态共建:打造工业视觉的"安卓系统"
迁移科技构建的开放生态包含:
-
技术适配层:
- 已对接KUKA、ABB等20+机械臂品牌
- 支持95%主流工业通讯协议
-
服务保障网:
- 48小时现场响应机制
- 7×24小时远程诊断中心
- 年度系统健康度检测
-
人才培养体系:
- 每月定期开展认证工程师培训
- 开发可视化调试教学系统
结语:通往智能制造的新里程碑
当某重型机械制造厂的成功案例显示,通过部署迁移科技系统,其大型铸件的搬运损伤率从3.7%降至0.02%;当某精密电子企业凭借Pixel Mini实现0.1mm级元器件的稳定抓取——这些数字背后,是工业视觉从"可用"到"可靠"的质变突破。
迁移科技正在用"视觉智能+工业know-how"的独特路径,重新书写机器人上下料领域的技术标准。我们诚邀全球合作伙伴共同探索:
- 如何将交付周期压缩至传统方案的1/3?
- 怎样实现新场景方案的平均验证周期≤72小时?
- 何时能突破50次/小时的行业节拍新纪录?
答案,就在下一次技术革新的现场。