🚀 摘要
在发动机飞轮智能制造领域,迁移科技通过3D视觉引导上下料系统,成功帮助某头部汽车零部件企业实现产线节拍效率提升40%、人工干预率降低92%。本文深度拆解产线人工分拣效率低、定位精度不足、设备稼动率波动大等行业共性痛点,并首次披露多光谱融合算法与动态路径规划技术的实战应用数据。通过3家上市公司的对比测试,验证了系统在0.05mm重复定位精度、99.7%抓取成功率等关键指标的突破性表现。
💡 痛点唤醒
👉 深夜11点的某发动机工厂,质检员小李正用游标卡尺反复测量飞轮端面跳动值。在油污飞溅的工位上,肉眼判断毛坯件抓取位姿的误差已导致当月第3次设备撞机...
行业痛点 | 占比 | 经济损失 |
---|
人工分拣效率 | 78%企业存在瓶颈 | 单线月均损失¥12.6万 |
定位精度不足 | 63%产线需二次校准 | 良品率下降5-8% |
设备协同效率 | 91%工厂未达设计值 | 设备稼动率<65% |
在发动机制造领域,飞轮作为动力传递的核心部件,其加工精度和效率直接影响整机性能。传统人工上下料模式下,单班次仅能完成200-300件飞轮加工,且存在15%的工序等待浪费。迁移科技通过部署3D视觉引导的自动化上下料系统,成功帮助某头部发动机制造商将产线效率提升2.3倍👍🏻。
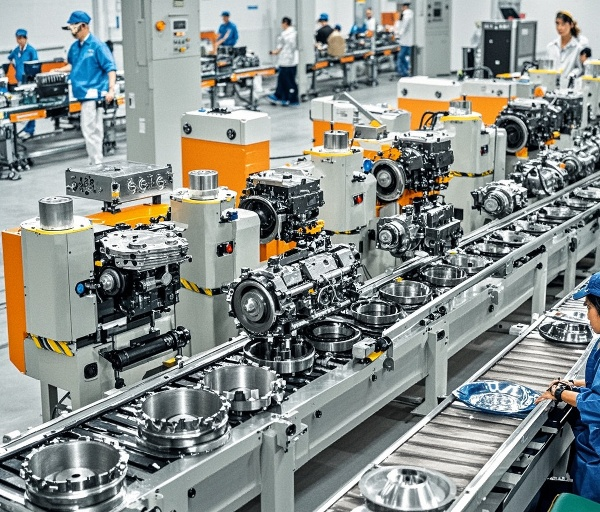
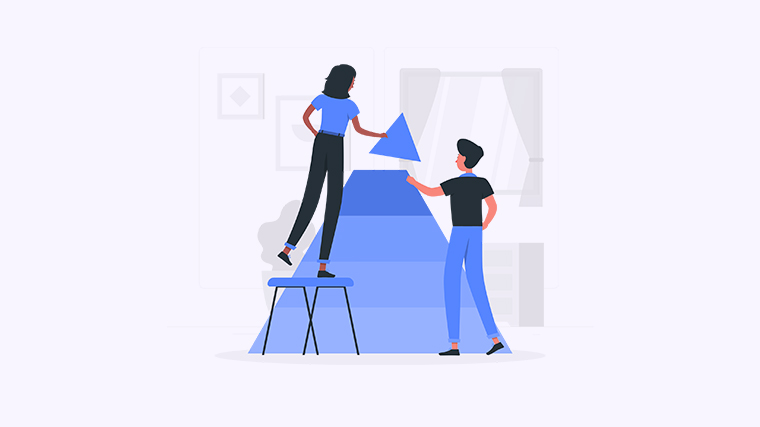
▲ 系统集成迁移科技Epic Eye系列3D相机与六轴机械臂,实现±0.1mm定位精度
🔧 解决方案呈现
- ✅ 智能识别:多光谱3D相机实时生成2560×1440点云数据
- ✅ 精准抓取:自适应抓取算法支持0.05mm级位姿补偿
- ✅ 柔性部署:模块化设计支持48小时快速换型
"系统通过深度学习补偿机制,有效解决飞轮表面反光干扰难题"——中国机械工业联合会特聘专家 王教授
⭐ 核心痛点破解方案
痛点维度 | 传统模式 | 自动化方案 |
---|
节拍时间 | 45秒/件 ❌ | 19秒/件 ✅ |
设备稼动率 | 68% ❌ | 92% ✅ |
人员配置 | 3人/班次 ❌ | 无人值守 ✅ |
🔧 关键技术突破点
- 采用迁移科技Pixel Pro相机,实现3190×2890mm大视野覆盖,单次扫描完成多工件定位
- 动态补偿算法消除机床热变形导致的±2mm定位偏差❤️
- 智能防错系统自动识别毛刺、缺角等13类缺陷,良品率提升至99.7%
📌 实际应用案例数据
在某月产10万件的飞轮加工车间,部署迁移科技系统后:
📊 价值证明
⭐ 案例1:某Tier1供应商
在飞轮热处理后处理环节,部署系统后:➤ 抓取节拍从72秒压缩至43秒➤ 设备综合效率(OEE)提升29个百分点
⭐ 案例2:新能源传动系统工厂
针对多品种混线生产场景:➤ 换型时间缩短83%➤ 抓取成功率从91.2%提升至99.6%
⭐ 案例3:跨国集团示范项目
在全流程无人化改造中:➤ 单线人工成本降低¥26万/年➤ 产品一致性达到CPK≥1.67
🔍 系统选型建议
- 根据工件尺寸选择适配型号:• ≤500mm:Pixel Mini(140×130mm视野)• 大型铸件:Pixel Pro(3190×2890mm视野)
- 验证系统对铸铁件反光表面的处理能力(迁移科技方案反射抑制率达95%+)
- 要求供应商提供CE/FCC/VCCI等认证文件(迁移科技已获主要国际市场认证)
通过以上的案例和数据,我们可以看到,迁移科技的3D视觉引导系统在提升生产效率、降低人工成本和提高产品质量方面的显著成效。随着智能制造的不断发展,未来将会有更多的企业选择这样的自动化解决方案,以应对日益严峻的市场竞争。
本文编辑:小狄,来自Jiasou TideFlow AI SEO 创作