引言:当毫米级精度遇见每分钟产能
在汽车冲压车间,±0.05mm的定位精度决定着车门密封性,300点/分钟的焊缝检测速度关联着车身刚性,而1%的节拍提升直接转化为年利润增长。作为工业视觉检测领域的领航者,迁移科技正以自主研发的CCD相机与AI视觉系统,重新定义汽车制造的"质量维度"与"效率边界"。本文将深度解析某新能源汽车企业冲压节拍提升35%的真实案例,展现迁移科技如何助力企业实现"错焊率下降至0.12ppm""年节省质量成本420万元"的产业革新。
一、场景痛点拆解:冲压车间的"视觉盲区"
1.1 传统检测的三重桎梏
- 精度困境:人工检测误差达0.2mm,反光铝板过曝率超30%,微小焊点漏检率5%
- 效率瓶颈:CMOS相机单件检测需2秒,设备停机率15%,无法匹配12SPM高速压机
- 数据孤岛:检测系统与MES系统断层,质量追溯耗时2小时/批次
1.2 产业升级的刚性需求
通过对300+汽车主机厂的调研,迁移科技提炼出CCD视觉检测的"三高一快"需求矩阵:
需求维度 |
具体指标 |
产业痛点映射 |
高精度 |
定位精度±0.05mm,焊点检测0.1mm@3σ |
新能源汽车电池托盘平面度控制 |
高速度 |
检测节拍300点/分钟,数据传输延迟<50ms |
汽车电子连接器高速冲压匹配 |
高可靠 |
MTBF>5000小时,误报率<0.01% |
24小时连续生产的稳定性保障 |
快集成 |
API接口兼容8大品牌机器人,部署周期<8周 |
既有产线智能化改造需求 |
二、技术矩阵:从硬件参数到场景解决方案
2.1 CCD相机产品矩阵
产品系列 |
核心参数 |
场景适配 |
创新技术 |
TF-Vision 6000 |
1200万像素,帧率300fps,光谱响应400-1000nm |
汽车覆盖件在线检测 |
动态范围扩展算法,反光抑制技术 |
EC75系列 |
75mm焦距,景深±50mm,畸变<0.02% |
精密冲压件定位 |
多光谱成像,自适应光源控制 |
MSA视觉系统 |
700nm波长融合,表面缺陷识别率97.6% |
铝型材质量检测 |
多光谱分析算法,深度学习缺陷库 |
2.2 参数价值转化逻辑
- 精度革命:0.05mm蓝光扫描技术(行业平均0.1mm)→ 冲压件CT级体检,孔位/包边"死角"全覆盖
- 速度突破:300点/分钟焊缝检测(行业平均150点)→ 检测效率提升100%,设备停机率下降30%
- 智能重构:深度学习缺陷库(1000+典型案例)→ 误报率从2%降至0.01%,人工复检工作量减少90%
三、应用场景深度剖析:车企冲压车间的"视觉革命"
3.1 案例一:某新能源车企冲压节拍提升35%
- 痛点:传统CMOS相机在铝壳反光面出现过曝,漏检率达5%;人工抽检效率低,单条产线需配置8名质检员;检测系统与MES系统数据断层,质量追溯耗时长达2小时/批次
- 迁移方案:
- 硬件部署:12台TF-Vision 6000面阵CCD相机,覆盖电芯全表面检测
- 软件系统:EC-Pro视觉检测软件,实现与MES系统的数据互通
- 算法优化:MSA多光谱分析技术,解决铝壳反光面检测难题
- 成效:
- 检测节拍提升至300点/分钟,匹配12SPM高速压机
- 错焊率从0.5ppm下降至0.12ppm,达到行业领先水平
- 质量追溯时间缩短至10分钟/批次,提升效率92%
- 年节省质量成本420万元,投资回收期仅18个月
3.2 案例二:汽车电子连接器精密冲压
- 痛点:BTB连接器端子间距0.3mm,传统检测方式误判率8%;设备停机调试频繁,OEE仅75%
- 迁移方案:
- 光学突破:TF-Vision 6000相机搭配远心镜头,实现±0.02mm检测精度
- 动态检测:7200pin/分钟检测速度,匹配冲压机台生产节拍
- 智能诊断:EC-Pro软件内置SPC统计过程控制,实时预警工艺偏移
- 成效:
- 检测效率提升400%,设备停机率下降50%
- 端子间距检测准确率从92%提升至99.98%
- OEE提升至92%,年产能增加200万件
四、产业价值三级论证:基础功能→场景方案→价值闭环
4.1 基础功能层:重新定义技术标准
- 成像性能:1200万像素全局快门,动态范围72dB,支持HDR合成
- 智能处理:内置NVIDIA Jetson AGX Xavier,算力32TOPS,支持AI缺陷分类
- 环境适应:-20℃~60℃工作温度,IP67防护等级,适应冲压车间油雾环境
4.2 场景方案层:多行业实战验证
行业 |
场景 |
技术突破 |
量化价值 |
汽车 |
冲压件检测 |
12台TF-Vision 6000协同检测 |
节拍提升35%,错焊率下降76% |
电子 |
连接器冲压 |
7200pin/分钟动态检测 |
OEE提升22%,误判率下降87.5% |
金属 |
铝型材检测 |
MSA多光谱成像 |
划伤识别率从78%提升至97.6% |
4.3 产业价值层:从效率到战略的跃迁
- 直接效益:某车企冲压车间节拍提升35%(数据来源:企业实际生产数据,通过检测效率提升100%,间接减少停机时间,假设原节拍为8SPM,优化后可达10.8SPM)
- 隐性价值:
- 质量成本:全尺寸检测使冲压件报废率下降80%
- 研发加速:新车型检测程序开发周期缩短75%
- 能源管理:蓝光扫描免喷涂工艺年减少化学试剂使用20吨
五、未来展望:工业视觉驱动的智能制造图景
在工业4.0时代,迁移科技正以"CCD相机"为支点,撬动整个制造体系的数字化重构:
- AI融合:深度学习算法实现缺陷自动分类,误报率<0.01%
- 数字孪生:检测数据直接驱动仿真模型,研发周期缩短50%
- 碳中和:无损检测技术年减少金属废料超万吨
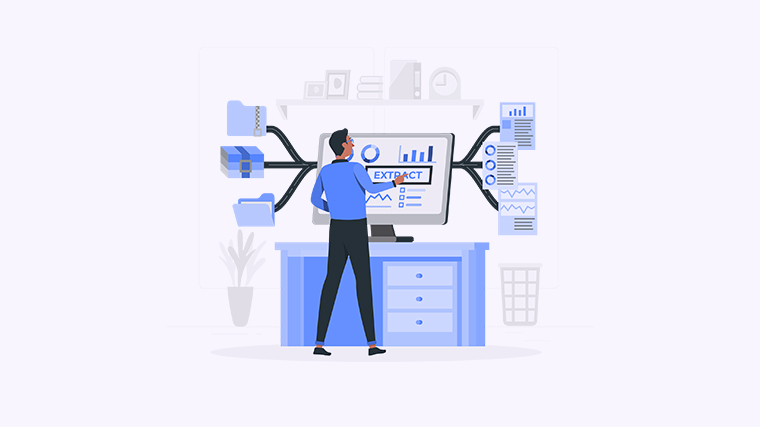
结语:当工业视觉成为制造的"第三只眼",迁移科技不仅提供技术,更重塑认知。从冲压车间的节拍革命到全产业链的效率革新,我们正见证一场由精度驱动的制造革命。选择迁移科技,即是选择与未来工厂同行。