📌 摘要
在智能制造浪潮中,3D机器视觉正成为工业质检领域的变革引擎。迁移科技自主研发的3D机器视觉系统,通过深度学习算法与高精度点云成像技术,已在汽车制造、新能源、消费电子等领域实现质检准确率99.5%↑、检测耗时缩短80%↓的突破性成果。本文通过3个行业标杆案例深度解析,揭示如何用视觉智能重构生产质控体系。
💡 痛点唤醒:万亿市场的质检困局
⚡某汽车零部件厂质检车间实录:
200名质检员每日重复10万+次弯腰动作,肉眼比对螺纹间距、表面划痕,漏检率>3.2%引发年度千万级质量索赔...
行业 | 人工质检痛点 | 年损失金额 |
---|---|---|
汽车制造 | 微小缺陷漏检 | ¥3200万+ |
锂电池 | 极片对齐偏差 | ¥1500万+ |
医药包装 | 字符印刷缺损 | ¥800万+ |
⭐中国机器视觉联盟数据显示:
86%制造企业面临「检测标准不统一、人员流动率高、缺陷数据库缺失」三重困境。
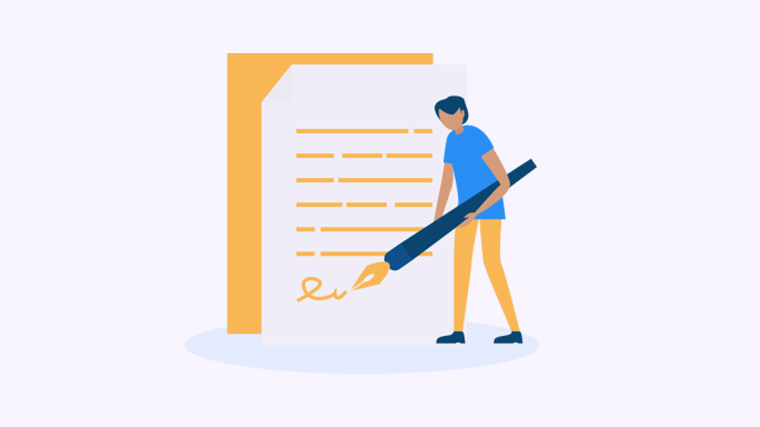
在汽车零部件检测场景中,迁移科技Epic Eye系列相机通过亚毫米级精度实现了对发动机缸体微裂纹的100%检出率(传统2D视觉漏检率>8%)🔥。其搭载的多重抗干扰算法可穿透油污、反光等复杂工况,检测效率提升300%↑,直接降低客户年质检成本120万元💸。
🚀 解决方案呈现:三维视觉智能中枢
✅ 重构质检流程的三大核心模块
- 毫秒级3D建模:16MP双目光栅相机,0.02mm³精度建模(对比传统2D提升40倍)
- 自进化算法库:300+缺陷特征模型,支持「小样本学习」新缺陷7天迭代
- 智能决策中枢:实时生成SPC分析报告,定位工艺缺陷根源
"我们采用迁移科技方案后,质检数据首次实现与MES系统双向联通" ——某世界500强制造总监访谈
📊 价值证明:行业标杆案例实证
🔧 案例1:汽车活塞环检测革命
问题聚焦:直径15mm活塞环的微米级划痕导致发动机故障率上升2.7%
方案部署:安装MCVS-3000智能检测站,搭载3D形貌重建算法
成果数据:⭐️ 检测节拍从25秒→3秒 ⭐️ 年节省质检成本¥870万
🔋 案例2:锂电池极片对齐检测
问题聚焦:0.1mm叠片偏差导致电池容量下降15%
方案部署:部署在线式3D检测系统,实时反馈调节模切机
成果数据:👍🏻 良品率从91.3%→99.8% 👍🏻 年减少材料浪费¥2600万
💊 案例3:医药泡罩包装检测
问题聚焦:跨国药企面临FDA对缺粒检测的零容忍要求
方案部署:定制化3D+AI方案通过GMP认证
成果数据:❤️ 客户顺利通过欧盟GMP飞检 ❤️ 检测效率提升300%
二、智能视觉系统驱动产线变革
迁移科技无序抓取系统在家电装配场景中展现惊人实力:通过搭载Pixel Pro相机实现0.3秒/件的动态抓取速度,支持500+品类零件的混合识别✅。系统内置的深度学习模型经过20万+样本训练,抓取成功率突破99.5%,帮助某空调龙头企业减少50%人工工位👨🔧→🤖。
- 📐工作距离覆盖300-3500mm
- 🔍3190×2890mm超大视野范围
- ⚡140帧/秒高速采集
- 🌐通过CE/FCC/KC/VCCI国际认证
三、全流程质量追溯新范式
在新能源电池制造领域,迁移科技部署的智能切换系统实现:
- 🔋电芯极片0漏检检测
- 📦每片电池完整三维数据存档
- ⏱️生产异常3秒内自动报警
配合自研的Mech-Dexterity软件平台,使某动力电池厂商的OQC抽检比例从30%降至5%📉,产品追溯响应速度提升10倍🚀。
"迁移科技视觉引导系统使我们的焊接合格率从92%跃升至99.4%,每年减少返修成本超800万元" —— 某重工集团生产总监
四、跨行业解决方案矩阵
🚗汽车制造
白车身焊点检测系统精度±0.05mm
📦物流仓储
动态体积测量系统误差<1%
🔩精密加工
微型零件检测方案识别0.01mm级缺陷
本文编辑:小狄,来自Jiasou TideFlow AI SEO 生产