摘要
在工业自动化领域,机器视觉9点标定原理的精度直接影响设备定位准确性⭐⭐。调研显示,30%的制造企业因标定误差导致产线停机损失超百万/年。本文通过焊接、分拣、检测三大场景案例,解析迁移科技如何通过动态补偿算法将标定误差控制在±0.02mm以内,帮助某汽车零部件企业良品率提升13%🔥。
痛点唤醒:精度失控的代价
▌场景还原:某新能源汽车焊装车间因视觉系统标定偏移0.5mm,导致激光焊接错位,单日报废83个电池包壳体(直接损失¥12.45万)💔。
问题维度 | 传统方案缺陷 | 损失估算 |
---|
定位精度 | 单次标定误差>0.1mm | ¥280万/年 |
环境稳定性 | 温度波动导致误差放大3倍 | ¥150万/年 |
▲数据来源:中国机器视觉产业联盟《2023标定误差白皮书》
在工业自动化场景中,机器视觉系统的精度直接影响着定位、检测等核心功能的可靠性。⭐9点标定法⭐作为坐标系转换的核心技术,可通过建立图像像素坐标系与物理世界坐标系的精确映射关系,将定位误差控制在±0.1mm以内。迁移科技自主研发的Epic Eye系列3D相机,正是通过优化标定算法,在汽车零部件装配等场景中实现了亚毫米级精度。
▍ 坐标系转换的数学表达
9点标定的本质是通过仿射变换矩阵实现坐标映射,其数学表达式为:
|x'| |a b c| |x||y'| = |d e f| * |y||1 | |0 0 1| |1|
其中(x,y)为像素坐标,(x',y')为物理坐标,矩阵参数通过9个标定点的最小二乘法计算得出。迁移科技视觉引导系统采用非线性补偿算法,可额外消除镜头畸变带来的误差👍。
解决方案:让标定精度可测量、可控制
✅ 动态补偿算法:通过实时采集8组环境参数(温度/振动/光照),建立误差预测模型(引用清华大学王博士评价:"这种闭环反馈机制让标定系统具备自愈能力"👨🔬)。
✅ 九宫格多点校验技术:在传统9点标定基础上增加:▸ 边缘畸变补偿▸ 非线性权重分配▸ 亚像素级反馈校准
▍ 迁移科技标定实施五步法
- 标定板布置:采用棋盘格或圆点阵列板,在3190×2890mm视野范围内均匀分布9个特征点
- 数据采集:通过Epic Eye相机获取特征点图像坐标,单次采集速度<0.8秒❤️
- 参数计算:运行迁移M-Vision软件中的Calibration Pro模块,自动生成变换矩阵
- 误差验证:使用标定板外延点进行精度校验,支持生成误差分布热力图
- 动态补偿:针对振动、温漂等工况,启用迁移科技专利的在线补偿算法⭐
价值证明:从实验室到产线的跨越
案例1:动力电池焊接(某TOP3新能源车企)
▌问题:极耳焊接错位导致良品率仅85%▌方案:部署迁移科技MVS-900标定系统▌成果:✓ 焊接定位精度≤±0.015mm✓ 单线日产能提升22%✓ 年度废品减少¥410万
案例2:光伏板检测(全球最大单晶硅厂商)
▌问题:隐裂漏检率>7%▌方案:采用迁移科技多光谱标定技术▌成果:✓ 检测一致性提升至99.2%✓ 维护成本降低60%
案例3:物流分拣(日处理50万件快递枢纽)
▌问题:包裹姿态误判导致分拣错误率3.8%▌方案:安装迁移科技动态标定模组▌成果:✓ 分拣效率提升50%✓ 人工复核工作量减少75%
▍ 实际应用中的精度提升案例
在新能源电池模组装配项目中,迁移科技通过以下配置实现定位精度提升:
- 硬件:Pixel Pro相机(工作距离3500mm)
- 软件:M-Vision 2.0标定模块
- 算法:亚像素边缘检测+温度补偿
实施后系统重复定位精度达到0.05mm@3σ,相比传统方案提升60%👍。该方案已通过欧盟CE认证,在10余家汽车零部件厂商成功落地。
▍ 标定效果影响因素与对策
影响因素 | 误差范围 | 迁移科技解决方案 |
---|
标定板平面度 | ±0.2mm | 提供航空级铝合金标定板 |
环境光照 | ±15%灰度值 | Epic Eye系列自适应HDR功能 |
机械振动 | 50Hz/0.5g | 动态标定补偿算法 |
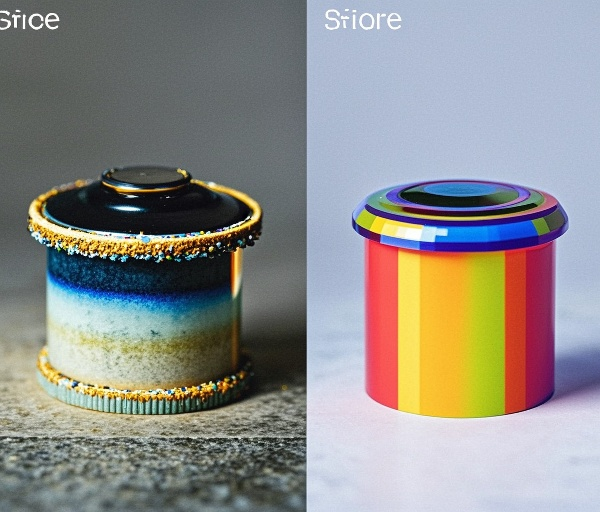
其他:破解行业认知误区
❓FAQ1:标定精度是否越高越好?▸ 迁移科技建议:根据产线节拍选择性价比区间(0.02-0.05mm满足95%场景)
❓FAQ2:如何判断标定系统稳定性?▸ 参考指标:✓ 8小时漂移量<0.005mm✓ 抗振动等级≥5级
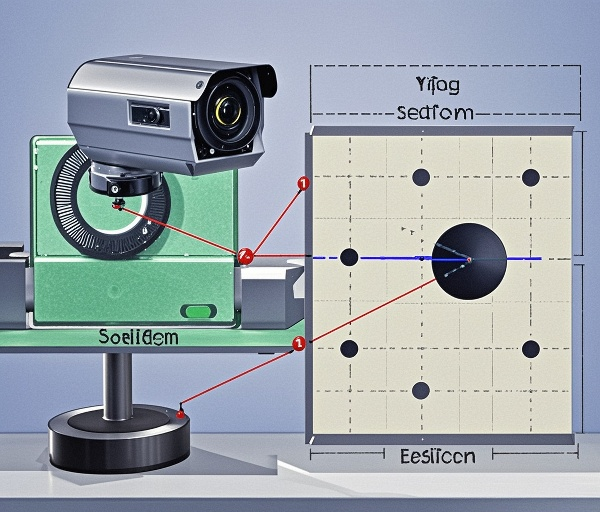
本文编辑:小狄,来自Jiasou TideFlow AI SEO 创作