在新能源汽车电池托盘焊接车间,传统焊接机器人正面临着前所未有的挑战:弧形工件的焊缝偏差导致焊接漏点,强光飞溅环境下传感器频繁误判,多型号混线生产时编程调试耗时长达 8 小时…… 这些场景折射出工业焊接领域的三大核心痛点:
- 精度挑战:铝合金薄板焊接要求焊缝偏差控制在 ±0.5mm 内,传统示教编程方式难以应对曲面工件的位置波动
- 环境干扰:焊接弧光辐射强度超过 10000lux,普通视觉传感器成像模糊,导致实时跟踪失效
- 柔性生产:新能源汽车多品种小批量生产模式下,人工示教编程效率低,换型时间占比超过 30%
北京迁移科技通过对 300 + 焊接生产线的深度调研发现,这些痛点本质上是 “传统视觉技术性能边界” 与 “智能制造升级需求” 的矛盾。当汽车主机厂追求 30JPH(每小时焊接件数)的高节拍生产,当工程机械行业需要应对 500kg 级重型构件的焊接变形,传统解决方案的局限性日益凸显。
迁移科技的 Epic Eye Pixel Mini 3D
视觉系统,以毫米级精度重构了机器人焊接的感知体系,其技术优势在实际场景中转化为可量化的价值提升:
技术指标 |
传统视觉方案 |
Pixel Mini 方案 |
实际价值提升 |
测量精度 |
±2mm |
±0.8mm(典型值) |
复杂曲面焊缝定位误差减少 60% |
抗环境光能力 |
<5000lux |
15000lux 稳定成像 |
焊接弧光环境下成像合格率提升 95% |
数据采集速度 |
1.2 秒 / 帧 |
0.2 秒 / 帧 |
高速运动工件实时跟踪成为可能 |
设备体积 |
200×150mm |
135×90mm |
狭小焊接空间安装适配性提升 40% |
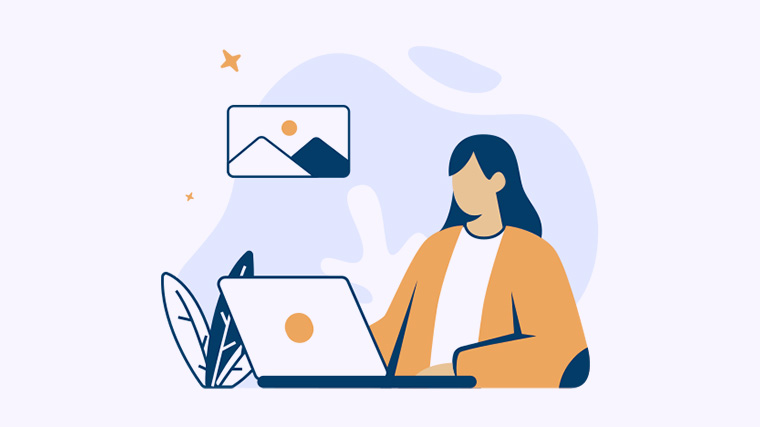
这款体积小于 iPhone 14 Pro Max 的工业相机,采用自研 DLP 编码技术,解决了透明反光工件的成像难题。在某新能源汽车电池壳焊接现场,即使面对阳极氧化处理的铝合金表面,依然能清晰捕捉 0.3mm 的焊缝特征,为机器人提供精准的位置补偿数据。
在工程机械臂架焊接场景,工件受焊接热变形影响,传统离线编程方案需要每 20 分钟人工校准一次。迁移科技的 3D
视觉系统通过 0.2 秒 / 次的高频数据采集,实时计算焊枪与焊缝的位置偏差,配合机器人运动控制算法,实现了 ±1mm 的动态跟踪精度。某三一重工焊接生产线实测显示,该方案将热变形导致的焊缝偏移不良率从 5.7% 降至 0.6%。
针对家电行业多型号压缩机壳体焊接需求,视觉系统内置的 AI 算法可在 3 秒内完成工件型号识别,并自动调取对应的焊接轨迹库。青岛某海尔工厂应用案例显示,该方案将换型调试时间从 45 分钟缩短至 8 分钟,支持单日 20 + 型号的混线生产,设备利用率提升 35%。
通过集成点云数据分析模块,系统可在焊接过程中实时监测熔池深度、焊缝宽度等关键参数。宁德时代电池模组焊接线引入该方案后,首次实现了焊接质量的 100% 在线检测,漏焊、焊穿等缺陷的检出率达到 99.9%,配合追溯系统形成完整的质量管控闭环。
在某比亚迪新能源汽车工厂的实践中,3D
视觉引导焊接方案创造了显著的综合效益:
- 效率提升:冲压车间焊接节拍从 12 秒 / 件提升至 8.5 秒 / 件,单条产线年产能增加 15 万台
- 成本节约:人工示教成本下降 70%,年度设备停机损失减少 260 万元
- 质量升级:关键焊缝一次通过率从 89% 提升至 98.7%,售后焊接相关投诉下降 82%
- 绿色制造:精准的焊接参数控制使焊丝消耗减少 18%,二氧化碳排放同步降低
这些价值提升背后,是迁移科技 “硬件 + 软件 + 算法” 三位一体的技术架构在发挥作用。自研的迁移 3D 视觉软件提供流程化操作界面,内置的 12 种智能算法覆盖 90% 以上的焊接应用场景,配合开放的 API 接口,实现与 ABB、KUKA、FANUC 等主流机器人的无缝联动。
作为中关村高新技术企业,迁移科技的技术创新始终锚定行业痛点:
- 研发投入:每年将 25% 的营收投入研发,累计获得 57 项专利,其中 3D 视觉抗干扰算法打破国际垄断
- 行业适配:针对汽车、重工、家电等不同领域,开发专用硬件模组和行业解决方案,如耐粉尘的 IP65 防护设计、高温环境散热优化
- 生态共建:与宁德时代、三一重工、海尔等龙头企业建立联合实验室,累计完成 127 个定制化项目,形成 “需求定义 - 技术研发 - 场景验证” 的闭环
在第六届浙江大学校友创业大赛中斩获一等奖的 “无序抓取” 技术,正是这种研发理念的产物。当该技术应用于焊接工件的上下料环节,配合 3D
视觉引导焊接,实现了从 “毛坯上料 - 定位焊接 - 成品检测” 的全流程无人化。某徐工集团起重机臂焊接线案例显示,该方案将人工干预频次从每班 200 次降至 15 次,真正实现了 “黑灯工厂” 的焊接场景。
随着工业 4.0 的深入,机器人焊接正迈向三个发展阶段:
- 数字化阶段(当前):实现焊接过程的可视化与数据采集
- 智能化阶段(3-5 年):基于 AI 算法的自主工艺优化
- 自适应阶段(5-10 年):具备自我学习能力的焊接系统
迁移科技的技术布局已提前卡位智能化阶段,其研发的 AI 焊缝识别算法,能够通过 10 万 + 焊接样本训练,自动识别 200 + 种焊缝缺陷模式,识别准确率达到 99.2%。这种 “数据驱动” 的技术升级,正在改写工业焊接的质量控制范式。
当制造业面临 “成本压力” 与 “品质升级” 的双重挑战,智能化改造已不是选择题,而是必答题。迁移科技愿以三大价值承诺,成为您的可靠伙伴:
- 技术可靠性:通过 SGS 认证的质量管理体系,确保设备年均无故障时间超过 8000 小时
- 服务敏捷性:7×24 小时响应机制,48 小时现场支持,3 个月项目交付周期
- 价值共创性:提供从方案设计到人员培训的全生命周期服务,助力客户实现 “投资回报率 18 个月回本” 的目标
在青岛海尔的智能工厂、在宁德时代的超级电池厂、在三一重工的灯塔车间,迁移科技的 3D 视觉技术正在重塑工业焊接的精准维度。我们相信,每一次毫米级的精度提升,都在积累着制造业转型升级的磅礴力量。
立即联系迁移科技,让 3D 视觉成为您焊接生产线的 “智能眼睛”,共同解锁工业制造的精准效率密码。